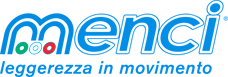
COMPOSITE MATERIAL PANELS COMPOSITE SANDWICH PANELS A LIGHT RECIPE FULL OF FLAVOUR...
23/09/2016
Composite sandwich panels are already widely used in both the Air force and aerospace, and even in rail transport, but their use on the market in the construction of tipper bodies has been limited, directed to non-structural components. Let’s take a step backward and discover what is this simple, genius technological innovation. The panel is made up of two skins in thin aluminium that form a casing to an inner core selected from aluminium honeycomb or foamed polymer in PET or PVC material. The PVC in this case is very strong and durable, while the PET is 100% recyclable and infinitely reusable. This introduction to the materials is a must because it is precisely their exact combination that represents the Menci technological revolution. Our research and development department has designed a panel revisiting all the individual components with highly innovative formulas aimed at reducing their weight, while at the same time improving their reliability in function of the destination of the panel itself. Even the manufacturing process of the body has been revised, as no welding is required for the construction of the panel, an innovation which opens a new world in terms of constructive solutions. The panels are in fact assembled to one another by means of structural adhesives selected ad hoc to resist intensive use in harsh weather environments and for transport and lifting of considerable sized loads (33 tons). COMPOSITE VEHICLES MENCI REVOLUTIONISES THE WORLD OF TIPPING BODIES Opening up new exciting scenarios yet to be explored, and design materials that go beyond aluminium and its traditional semi-finished products! A discovery, reveals the engineer in charge of the Research and Development team with more than a touch of enthusiasm, that is just as significant as the first application of aluminium instead of steel. The world of transport has always been looking for a reduction in tare. For 90 years, Menci has been committed to the ideal of light vehicles (minimum tare) at the service of reliability more than anyone else, creating continually lighter vehicles and first and foremost attempting to decrease the thickness of aluminium - which has always been considered the material with the best Resistance-Weight-Reliability ratio. It is at this point that the intuition of the Research & Development team arrives, directed by Pietro Menci who, assisted by prestigious chemical and metallurgical companies and universities such as Parma and Milan, understands that extruded semi-finished aluminium can be largely replaced by multilayer composite material sandwich panels redesigned specifically for the transport of tipping bodies or other types. Tests immediately gave incredible results, but it is from the analyses of FEM finished components (a set of simulations with computer to calculate tensions and deformations) that the team became fully aware of the reliability of the product and its amazing performance. The prototype was subjected to further tests on the road and crush tests which confirmed the theoretical analysis. If the decrease in tare of two hundred kilos (two quintals) can be considered an exciting result, the know-how acquired in the research and study of these new materials allows us to imagine even more incredible scenarios, as if only the tip of the iceberg has been scratched. Even if it is hard to imagine that one day Menci will be able to transport that entire iceberg, for the moment the first composite material vehicles designed are destined for the transport of bulk material (agricultural or palletized) in large volumes and for long distances. The subsequent move is to apply these new materials on the entire Menci bodies range, with specially designed, various type composite panels adapted for their various types of bodies and intended use.
Visit the site >>>